

Conversely, the mechanical properties of the parts appear to be uniform and stable. Moreover, the forging process has several limitations in producing precise parts and productivity because the forming process has multiple steps.
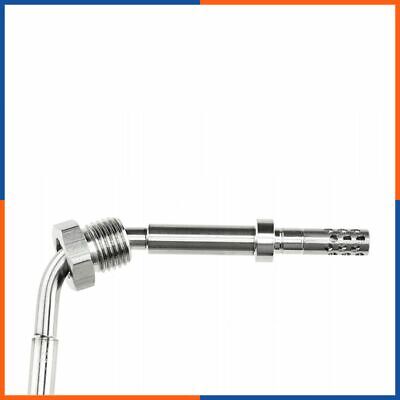
However, the process is inappropriate for producing parts with high strength requirements because defects such as turbulent flow-induced air entrapment could result as the melt flows into the mold cavities. The die casting process, that is, the forming process that fills mold cavities with molten metal, has advantages for the mass production of thin parts with complex shapes which have little need for mechanical strength. Forming processes such as casting and forging, hot forging, and low-pressure casting have allowed lightweight aluminum alloy-based component to be used in passenger cars, but they have not been adapted to mass-production due to a lack of product reliability, increased costs, and excessive initial investment. Recently, the car industry has required lightweight parts to improve gas mileage and mitigate the impact of damaging emissions on the environment, which are thought to contribute to depleting the ozone layer, increasing greenhouse gases, and producing acid rain. The EMS is an effective process to improve a feed stock in the rheo-forming process with improved mechanical properties. In addition, the effect of the vacuum-assisted method on the performance of rheo-forged products is introduced. A variety of simulation studies are conducted. The effects of several process and metallurgy parameters such as stirring current, stirring time, pouring temperature, forming pressure, tip velocity, fraction of primary phase, and its morphology and distribution, on the final products are reviewed and discussed.
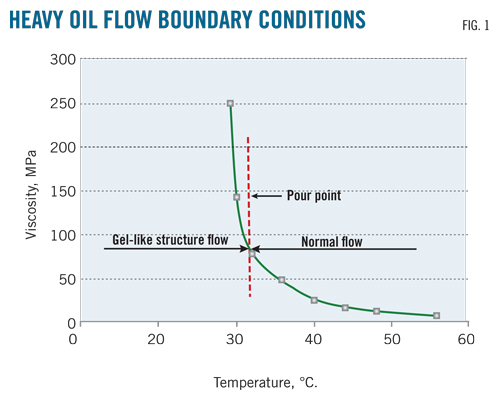
This paper describes a rheo-forming process for the development of automobile components, such as knuckle, by using rheology material with electromagnetic stirring (EMS) system equipment.
